Testimonials
For decades, we’ve been helping food processors, manufacturers and distributors simplify their operations with our ERP software. Our customer support is ongoing, and we love checking in with our customers to see what a big impact Canopy has had on their business.
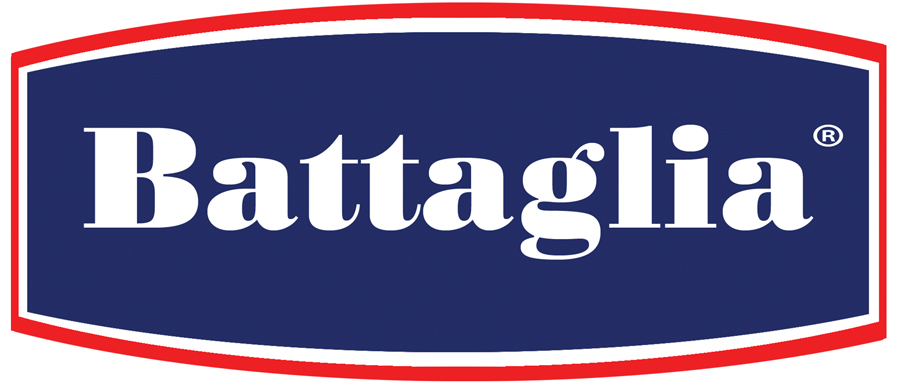
Battaglia Distributing
Food Distributor growing with Canopy and their partnership with Aspen Systems.
see more
Canopy is lightyears ahead of our previous ERP system. It has simplified and streamlined a lot of our day-to-day processes, which has allowed us to increase our customer base and product movement. Canopy provides a way to grow your business without also growing your expenses.
Testimonial video regarding Canopy software
Testimonial video regarding Aspen Systems
Testimonial video regarding Document Imaging
Testimonial video regarding Event Watch
Without Canopy we would still be living in the past. Canopy has helped us to realize a brighter future.
Joe Gariti, Chief Technology Officer
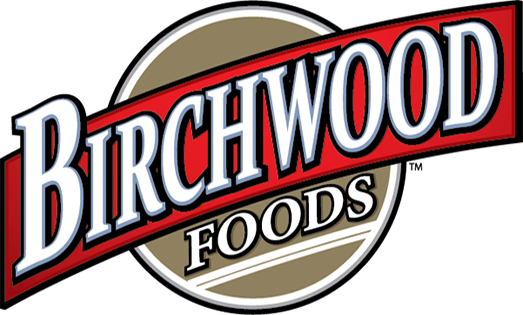
Birchwood Foods
Meat Processor keeps in the forefront of technological improvements.
see more
Aspen Systems successfully develops customer driven applications. They have a talented staff who analyze customer situations and provide effective solutions. Aspen has helped guide Birchwood Foods through two major system installations. We have confidence in their ability to keep us at the forefront of technological improvements. More importantly, they provide excellent customer service to solve issues that arise.
Aspen has helped guide Birchwood Foods through two major system installations.
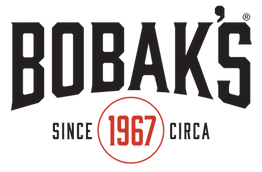
Bobak Sausage
Sausage Company grows with innovative production and warehousing features
see more
The flexibility of the Scanning system allows warehouse staff to be accurate and maintain proper controls. Inventory can be tracked whether it is lotted, non-lotted, a single case, a complete pallet, or a complete truckload, using variable weight or standard units of measures. Inventory is date driven and kept track of with the handheld scanners using slot locations to inform the warehouse workers regarding the location of the oldest product. Utilizing these innovative features, we have been able to manage our inventory.
We have been able to grow our business because of Canopy. Our partnership with Aspen Systems allows us to manage our growth with on-time accurate information.
Stan Bobak, President & CEO
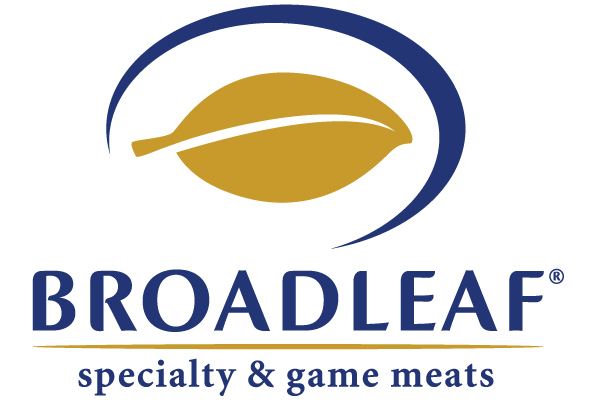
Broadleaf USA
Specialty Meats Processor & Distributor grows business and profits with Canopy.
see more
Broadleaf is a progressive company and we are always challenging ourselves and our business partners to raise the bar with regard to expectation, execution, and efficiencies. As the company grew, we came to the realization that our current software systems were placing limitations and restrictions on our forward planning and expansion of operations; it was time to identify an IT platform that better aligned with our growing business and the demands of the Food Industry.
While we sought and evaluated many different IT offerings and services, we decided to partner with Aspen Canopy. The driving factor for the decision was that Canopy took the existing multiple operating systems and brought those under the same umbrella, and at the same time, provided a robust level of support and guidance to improve the measurement and reporting applications. Our team members found Canopy to be user friendly, and after personalized training, everyone caught on quickly. Since the launch of Canopy, we have not looked back. Today, we continue to grow our business and financial vitals at higher levels. Broadleaf is proud to have Aspen solutions integrated into our business as we navigate future endeavors and opportunities.
Broadleaf is proud to have Aspen solutions integrated into our business as we navigate future endeavors and opportunities.
Mark Mitchell, President
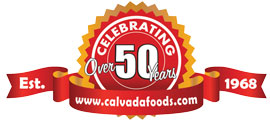
Calvada Food Sales
Food Distributor depends on Canopy’s Document Imaging for Accounts Receivable.
see more
Document Imaging is awesome for Accounts Receivable. If a customer claims they didn’t buy something, you are able to pull it up and say, Well your signature is right here. No more filing cabinets, no more paying somebody to file, no more file folders.
Testimonial video regarding Aspen Systems
Implementing Canopy went perfectly well. We closed business up on Friday night, we did our Implementation to Go-Live on Saturday, and by Sunday we were receiving just like we were any other Sunday. It was perfect.
Sarita Baker, Controller
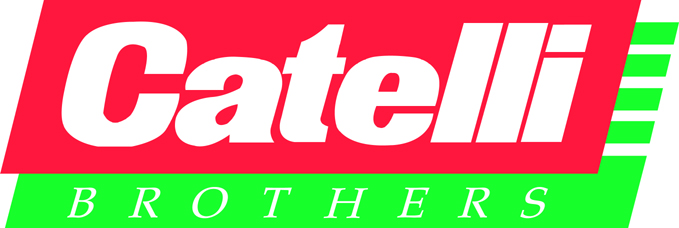
Catelli Brothers
Veal & Lamb Processor likes Aspen Systems’ Executive Conference and quality of Canopy.
see more
When I attended the Aspen Systems’ Executive Conference I was surprised to learn so many new ways that Canopy could improve my business. I immediately arranged for training sessions for my staff so they could take advantage of new features in the software. Catelli Brothers is truly diligent and dedicated to maximizing the use of Canopy for the benefit of our organization.
I was impressed with the advancements and all that Canopy has to offer and all the ways it could improve our business.
Anthony “Tony” Catelli, President & CEO
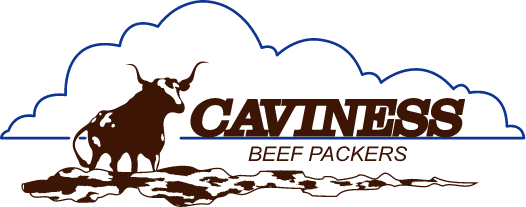
Caviness Beef Packers
Beef Processor streamlines their operation and improves efficiency significantly with Canopy.
see more
Our experience with Aspen Systems has been exceptional. Their solutions have streamlined our operations across all departments, from finance to inventory management, and helped us improve efficiency significantly. The user-friendly interface and powerful analytics tools give us real-time insights into our business performance, allowing us to make more informed decisions. The seamless integration with our existing systems and the flexibility of customization made it easy to adapt to our specific needs. We highly recommend Aspen Systems to any business looking to enhance productivity and drive growth.
We highly recommend Aspen Systems to any business looking to enhance productivity and drive growth
Tim Hobbs, Director of IT
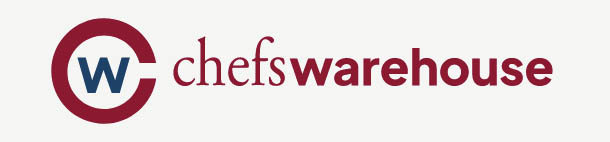
Chefs Warehouse
Center-of-Plate Protein Processor & Distributor drives growth and operational efficiencies with Canopy across multiple companies.
see more
From implementation, ongoing support and development of solution driven development, Aspen Systems is a true partner in ensuring our business systems are upholding our core values of customer service excellence. Through dynamic features and applications, we can drive operational accuracies and efficiencies while growing our business and profitability. The Aspen Systems team at every level of their organization is responsive, focused and aligned with our goals.
As we look at current features, updated or added functionality and custom development we can come together for comprehensive brainstorming that leads to dynamic solutions. Aspen Systems knows our specific business, our team members and our unique processes. We have navigated the growth of both our companies together and that familiarity allows us to work together efficiently with a true partner.
The Aspen Systems team at every level of their organization is responsive, focused, and aligned with our goals.
Robert Campion, Director
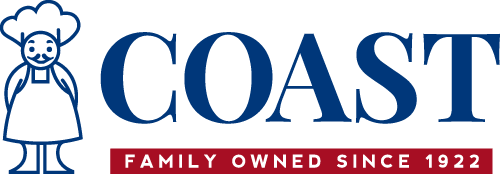
Coast Packing
Miscellaneous Foods Processor able to make quick business decisions.
see more
We had been searching for a system that would fit our needs for over 10 years and finally found that in the Canopy software by Aspen Systems. Aspen has provided our company a system that will grow with us and allows us to concentrate on our business rather than the software that helps run our business. The system is flexible and has provided us the reporting necessary to make quick decisions. The training and customer support has been truly exceptional.
We had been searching for a system that would fit our needs for over 10 years and finally found that in the Canopy software by Aspen Systems.
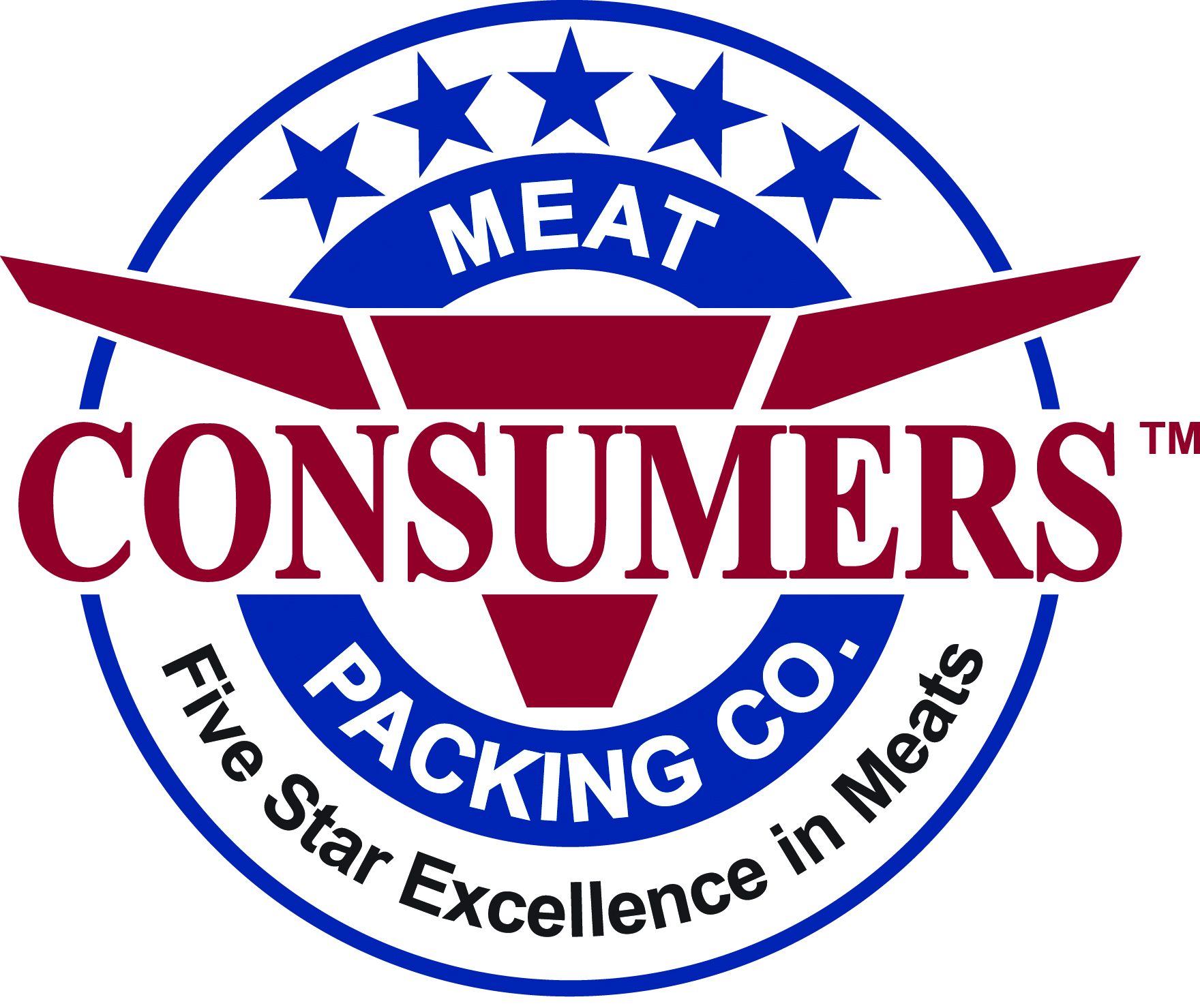
Consumers Packing
Protein Processor & Distributor gains complete control with Canopy.
see more
We were looking for software to continue our company growth. After reviewing our options, we chose Aspen. Through the use of the training, core modules, custom programming and the support desk, we have been able to fine tune Canopy to meet our company’s operations. We now have complete control of our operation from start to finish. I would recommend Aspen/Canopy not just for the software, but the key support we have received as well.
I would recommend Aspen/Canopy not just for the software, but the key support we have received as well.
Doug Wood, Controller
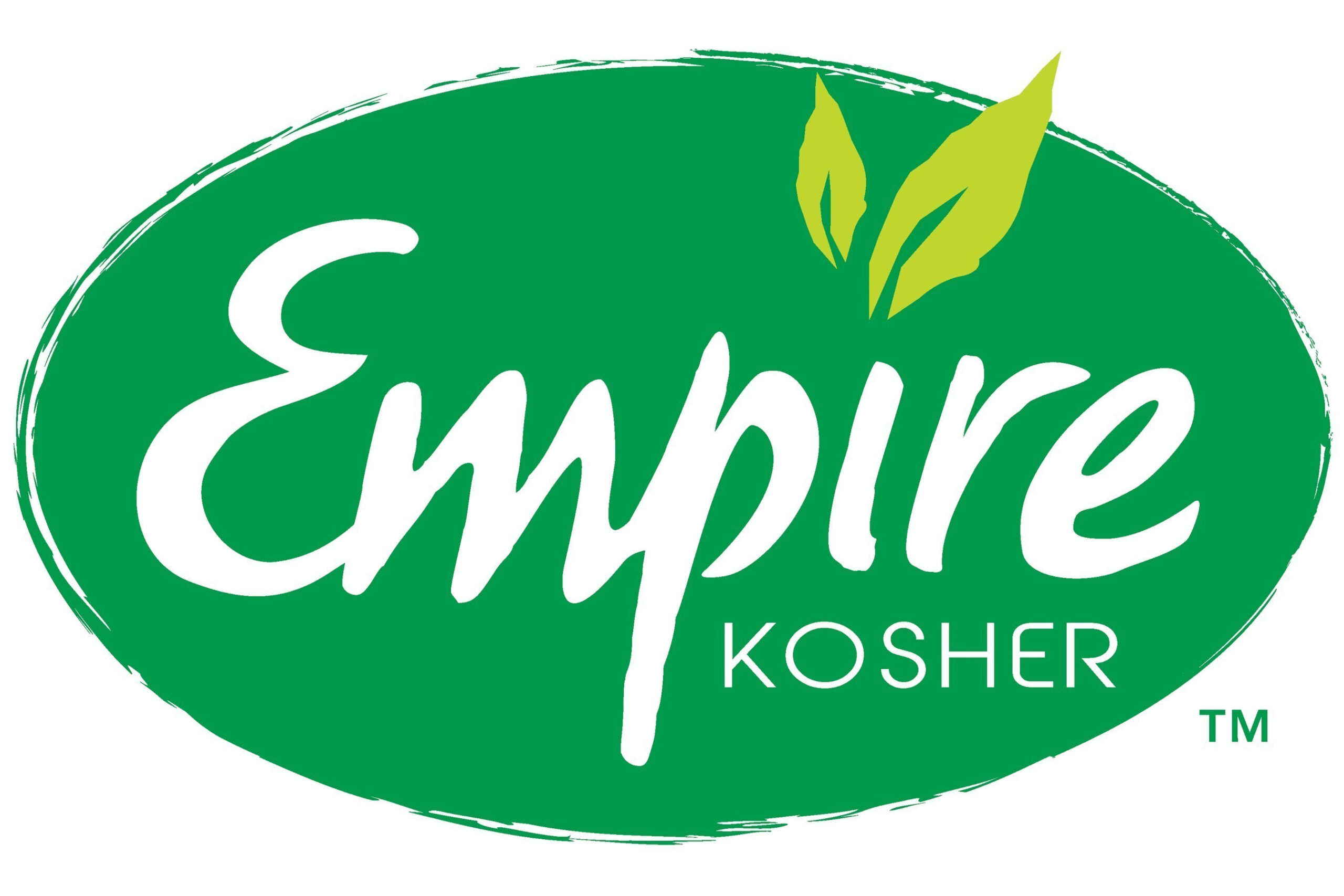
Empire Kosher
Kosher Poultry Processor utilizes Canopy’s full power of Aspen View Report writer.
see more
The Aspen View report writer is very easy to use and extremely useful. We have written and built a library of over 400 Aspen View reports that get the data we need presented in the exact format that we like. The Canopy Core modules, Aspen View, and the Report Scheduler all work together to ensure things are not falling through the cracks, but these products, in conjunction with Canopy’s Production module, support needs which are very specific to Empire Kosher Poultry.
We have written and built a library of over 400 Aspen View reports that get the data we need presented in the exact format that we like.
Todd Enders, IT Director
In-N-Out Burger
Meat Processor values Canopy’s reliability, product traceability, and partnership with Aspen Systems as they process their products for their restaurants.
see more
We have been using Canopy for fifteen years and have found it to be a highly reliable system backed by a skilled and accessible technical support team. Aspen Systems has been a valuable partner within our manufacturing operations.
Aspen Systems has been a valuable partner within our manufacturing operations.
Joe Azzaro, Director
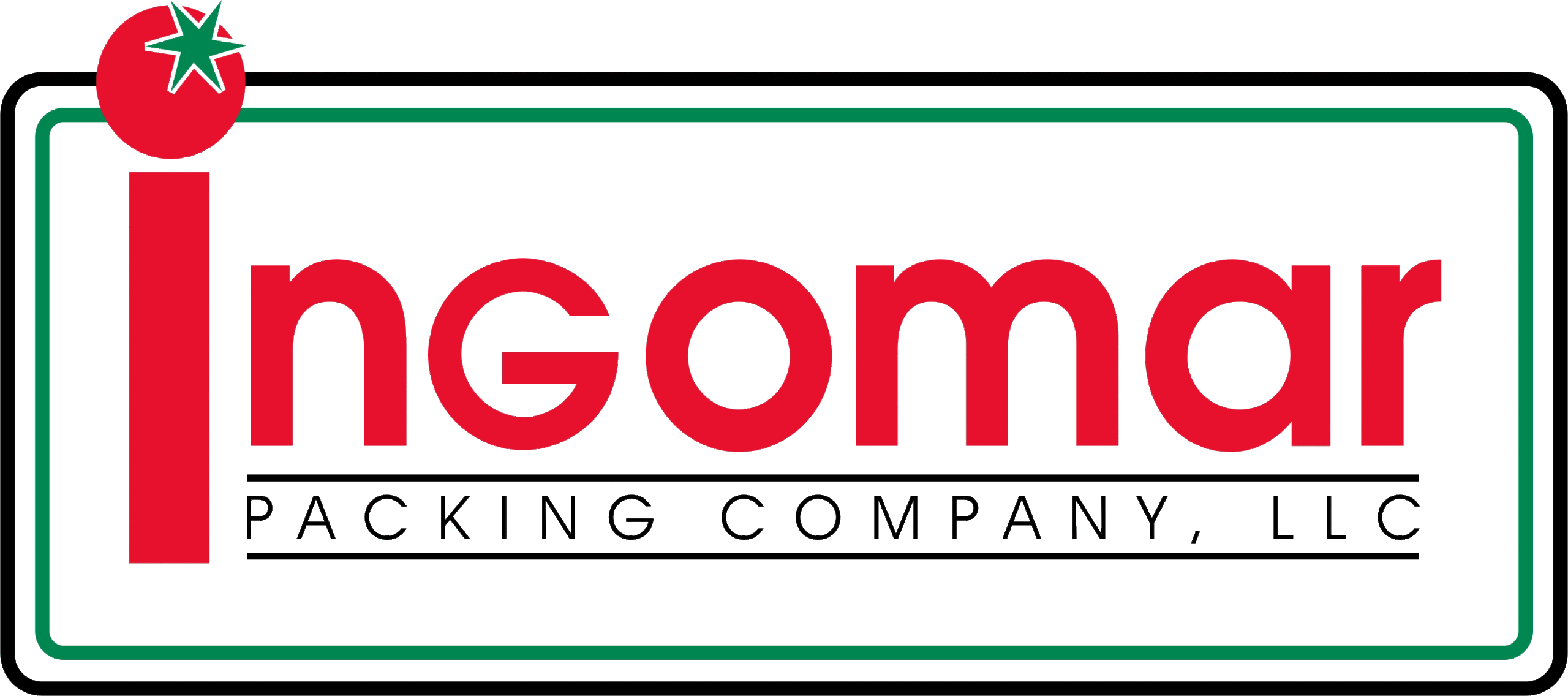
Ingomar Packing
Produce Processor utilizes Canopy for continual process improvement.
see more
Ingomar Packing has been a partner with Aspen Systems since 1994 and upgraded to Canopy in 2001. Ingomar has integrated many of their processes into Canopy including Financials, Order Entry, Payables, Quality Control, Tomato Production, Field System, and grower and customer contracts. Ingomar utilizes many Canopy Optional and Enhanced modules such as Data Capture, Labeling, Pulse, Event Watch, Production, and Document Imaging. We truly appreciate our partnership with Aspen Systems.
At the end of every season Ingomar and Aspen Systems meet to put together a list of ways that Canopy can improve Ingomar’s operations for the next season. This has been very beneficial to our organization.
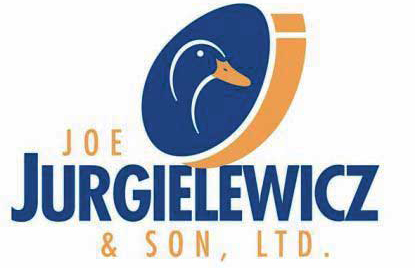
Joe Jurgielewicz & Son
Duck Processor takes full advantage of Canopy’s integrated scaling and labeling systems.
see more
Canopy provides us with information regarding what inventory is available for sale compared to what has been committed to a sales order. Canopy’s barcode scanning module also allows for tracking at the case level, which reduces mistakes in the shipping department. Now warehouse inventory is simply tracked by the case ID and pallet ID and transfers can be done by scanning the pallet ID. The result is a strong inventory system and traceability of product.
With Canopy’s fully integrated features in place, Joe Jurgielewicz is now able to focus on continued growth.
Dr. Joe Jurgielewicz, CEO
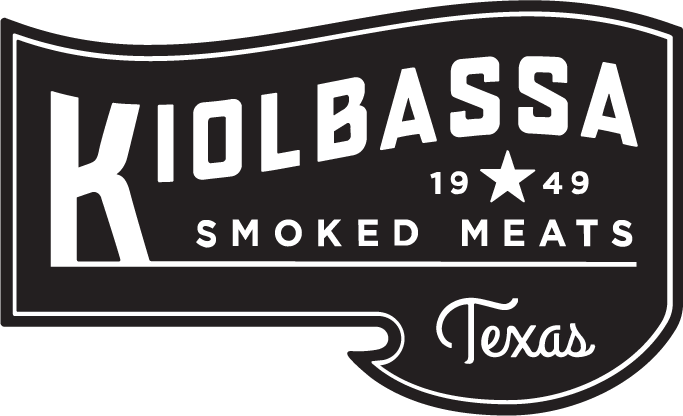
Kiolbassa Smoked Meats
Smoked Meats Processor transformed through quality assurance and Canopy’s seamless data.
see more
Using Canopy, Our Production and Quality Assurance team can monitor our production as well as quality assurance very efficiently. Canopy is able to perform “mock recalls” within 15 minutes to verify our quality control process. Temperatures are monitored automatically throughout the plants using Canopy’s Element module.
The dashboards have generated buzz with different teams, and now it seems that every department wants to monitor something different.
ERP Administrator
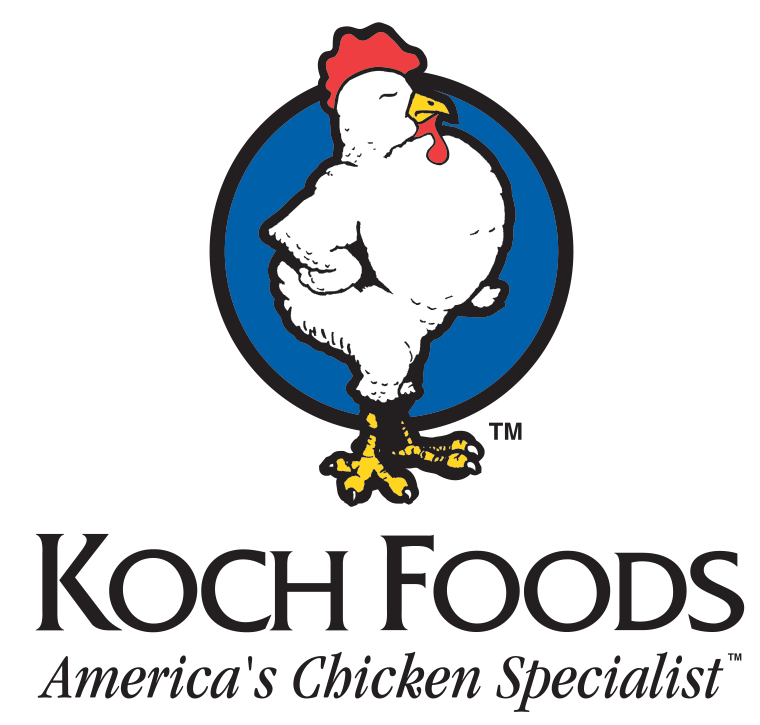
Koch Foods
Poultry Processor & Distributor manages extreme growth and long-relationship with Aspen Systems.
see more
Although scalability is a catch phrase used throughout business when referring to information systems, it is rare to find a technology organization that truly embodies that commitment. Not only has the software scaled to our needs throughout our growth process, but Aspen’s support and software services have scaled as well. The symbiotic relationship that Aspen and Koch have developed has allowed us to build a solid foundation for both current business operations and future growth.
After numerous hours of due diligence, the decision was made that Canopy and Aspen Systems was still the right choice for Koch.
Stewart Ward, VP of Information Systems
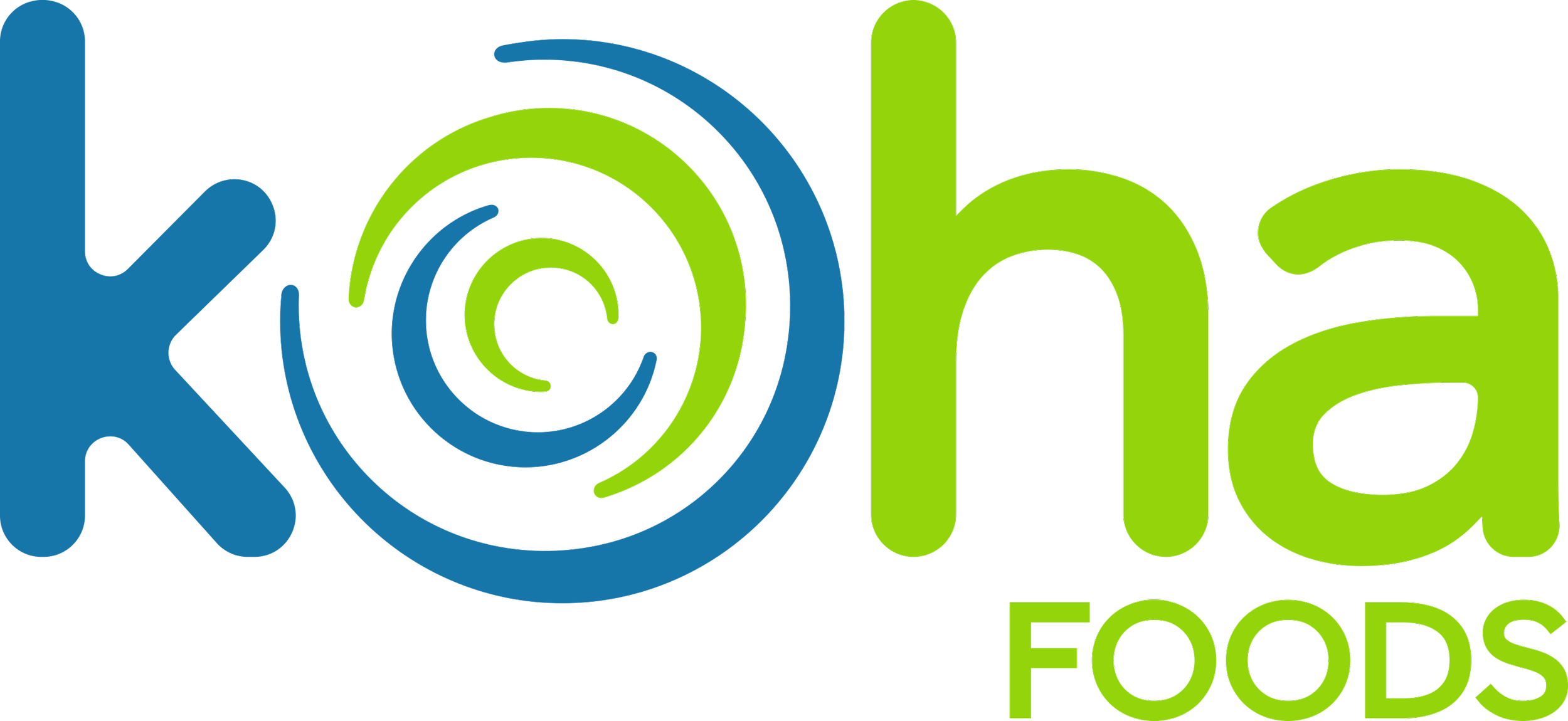
Koha Foods
Importer, Food Manufacturer, Distributor, & Exporter who takes full advantage of all that Canopy has to offer and its partnership with Aspen Systems.
see more
Koha Foods is a quality Asian food importer, food manufacturer, distributor, and exporter. Koha offers over 25,000 products to local Hawaiian businesses in addition to being one of the largest global exporters of Asian foods. Installing the Canopy software modules in 2016 allowed Koha Foods to have accurate inventory and timely information needed to run their business. Since implementing Canopy, they have grown substantially.
Testimonial video regarding Aspen View
Testimonial video regarding Document Imaging
Testimonial video regarding eCommerce
Testimonial video regarding Event Watch
We see everybody as a partner. Our customers are partners, our suppliers are partners, our vendors are partners. Canopy supplies information to all of them to help the supply chain work better
Dane Nakamura, CFO & COO
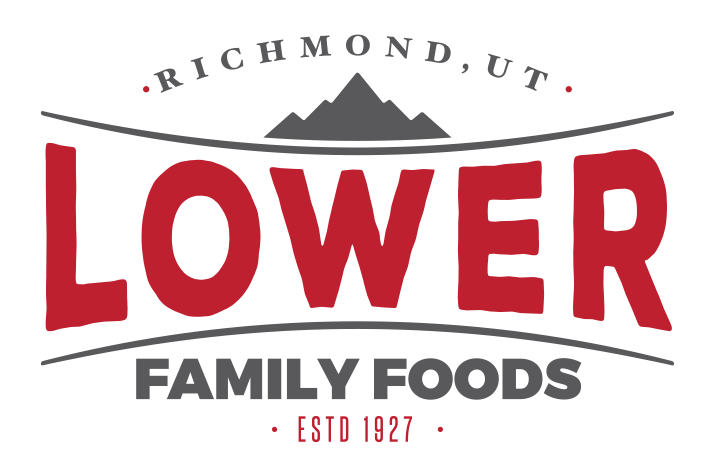
Lower Foods
Meat Processor benefits from expanded learning with Canopy.
see more
Canopy’s dashboard module Pulse, is very easy to use and intuitive. We easily created our own Inventory Dashboard and Scheduling Screen using Pulse, which has completely revamped our scheduling and production efficiency.
Data Capture, and specifically the flexibility of the Terminal Input stations, has made sourcing our products much quicker and easier. Traceability is a key premise throughout Canopy.
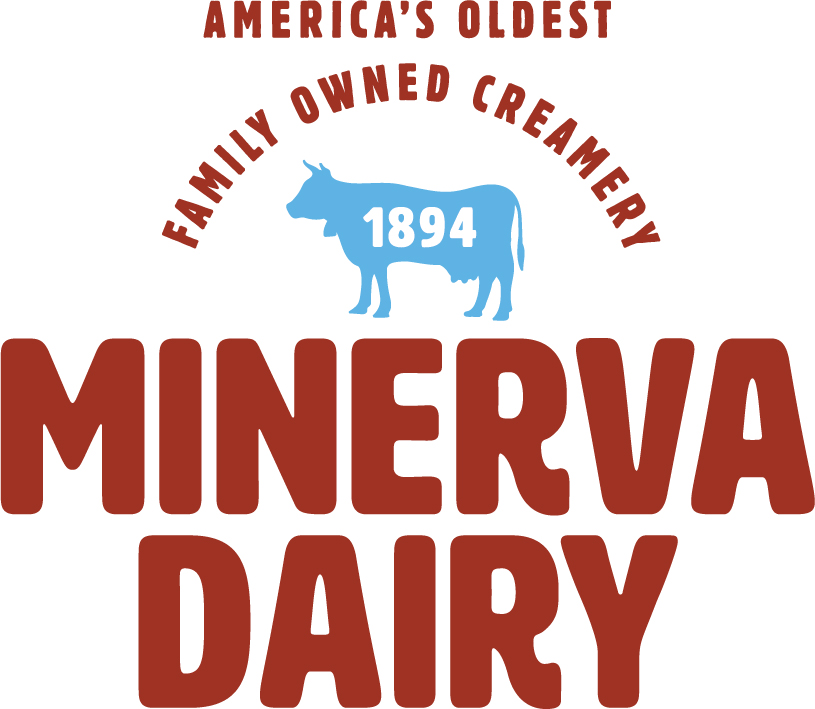
Minerva Dairy
Dairy Processor enhances processes with Canopy.
see more
Minerva Dairy relies heavily on Canopy’s Document Imaging module. Document Imaging is literally the greatest thing that ever happened to me. We just scan a document then toss it. Our office used to be filled with filing cabinets. Since implementing Document Imaging, so much room has been opened up that we have repurposed filing cabinets into extra storage space for non-paper items.
Canopy is a perfect fit for requirements in the Dairy industry. Minerva Dairy had very little need for customizations. They are constantly implementing new tools in Canopy to improve their processes. We went in thinking we could do X, Y, and Z and soon realized we can do the whole alphabet
Venae Watts, Co-Owner
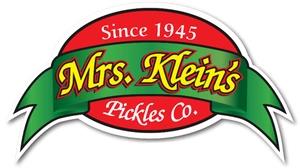
Mrs. Klein’s Kosher Pickle Company
Food Processor manages inventory to near perfection with Data Capture.
see more
Canopy is an exceptional system that offers comprehensive features. With just a few clicks, I can generate an instant inventory recall report. And with the decision to implement Data Capture, my warehouse team is able to produce and ship orders so much easier. My warehouse team have eliminated miss ships and shortages. Another thing I like about Canopy is how much better I’m able to manage my inventory levels. And finally, my inventory accuracy has improved to almost perfect.
My inventory accuracy has improved to almost perfect.
Jeff Knapp, Vice President
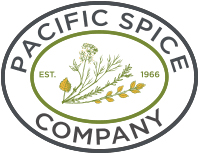
Pacific Spice Company
Spice Company takes advantage of integrated Canopy ERP to streamline production
see more
The Canopy ERP system has streamlined our order entry, and manufacturing, shipping, traceability and inventory processes. Canopy helps us manage over 4,800 products and 3,600 production formulas. We now better track our exact costs to manufacture each product. A key feature in Canopy occurs when customer orders are placed and a production work ticket is automatically created to manufacture finished products on the order that do not have enough stock.
Canopy has allowed Pacific Spice Company to improve their internal processes, have better and faster traceability of their inventory, grow their business, and have complete inventory control of their raw material, packaging, and finished products.
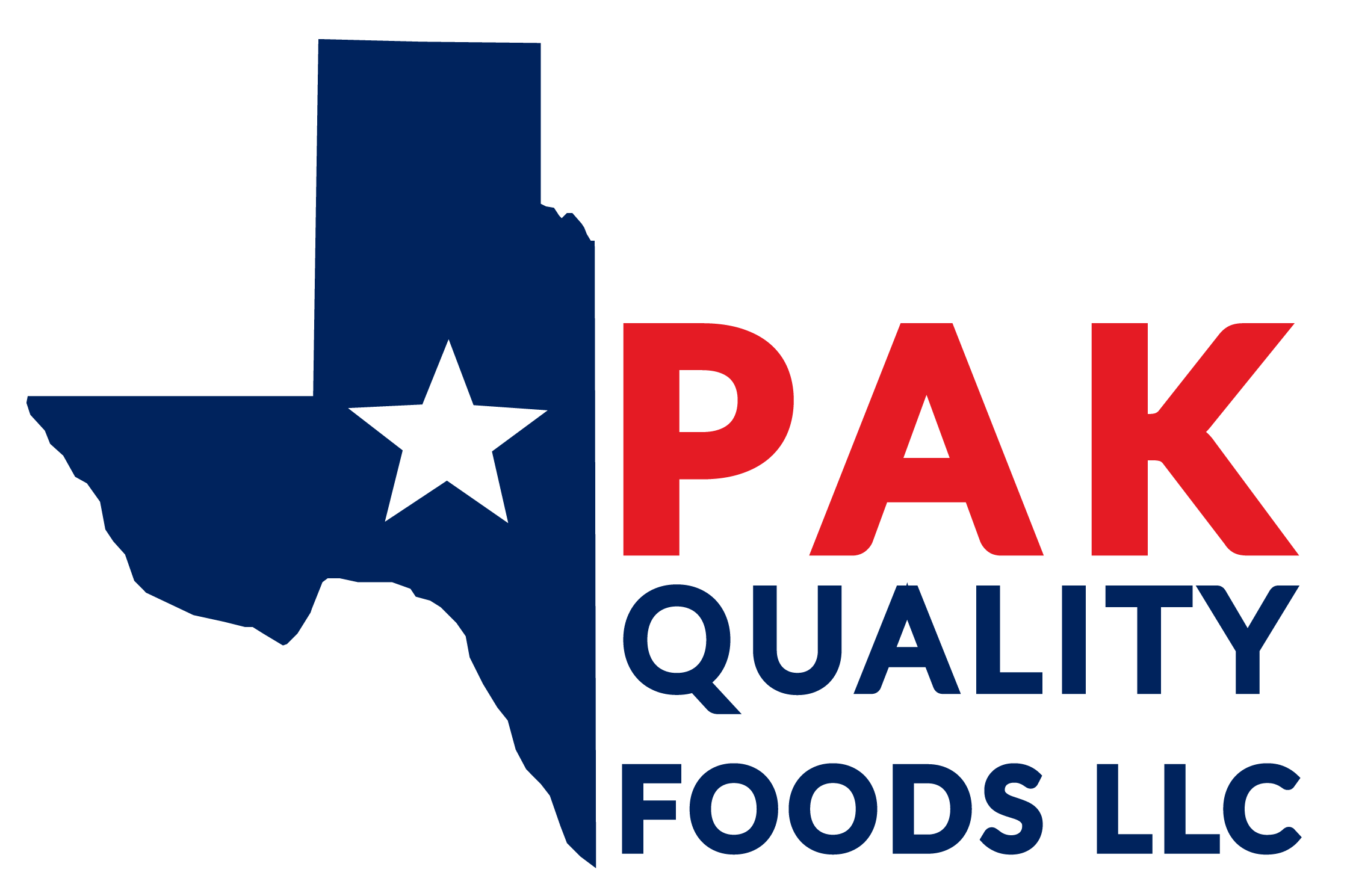
PAK Quality Foods
Broadline Food Distributor exceeds projected ROI with Data Capture.
see more
Before using Data Capture, we managed inventory and shipping manually. Data Capture has provided a significant improvement in inventory accuracy, reduced shipping and receiving errors, and tracking of returned product. Most importantly, it has increased our tonnage per hour per assembler. The return on investment has definitely exceeded our projections.
The return on investment has definitely exceeded our projections.
Terry L. Stokes, Controller
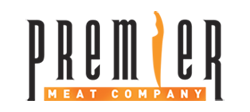
Premier Meat Company
Meat & Seafood Processor & Distributor improves operations and grows with Canopy.
see more
Premiere Meat Company is one of the leading Beef, Pork, Poultry, and Seafood processors on the west coast. Our growth came from being a one stop shop company providing our customers with different types of protein products along with ordering deadlines that are in-tune with the food industry. Canopy allowed us to make many improvements to our operations and easily increased our business thanks to our partnership with Aspen Systems.
Canopy’s Data Capture module gave the ability to have an accurate raw goods inventory, accurate finished goods inventory, and create a very efficient order filling method.
Harry Greenberg, Founder/CEO
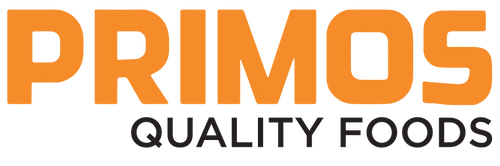
Primos Quality Foods
Food Distributor depends on Canopy for continued growth.
see more
We are more than satisfied with the Canopy system and it has been the back bone of our continued growth.
Abraham Arechiga, Chief of Operations
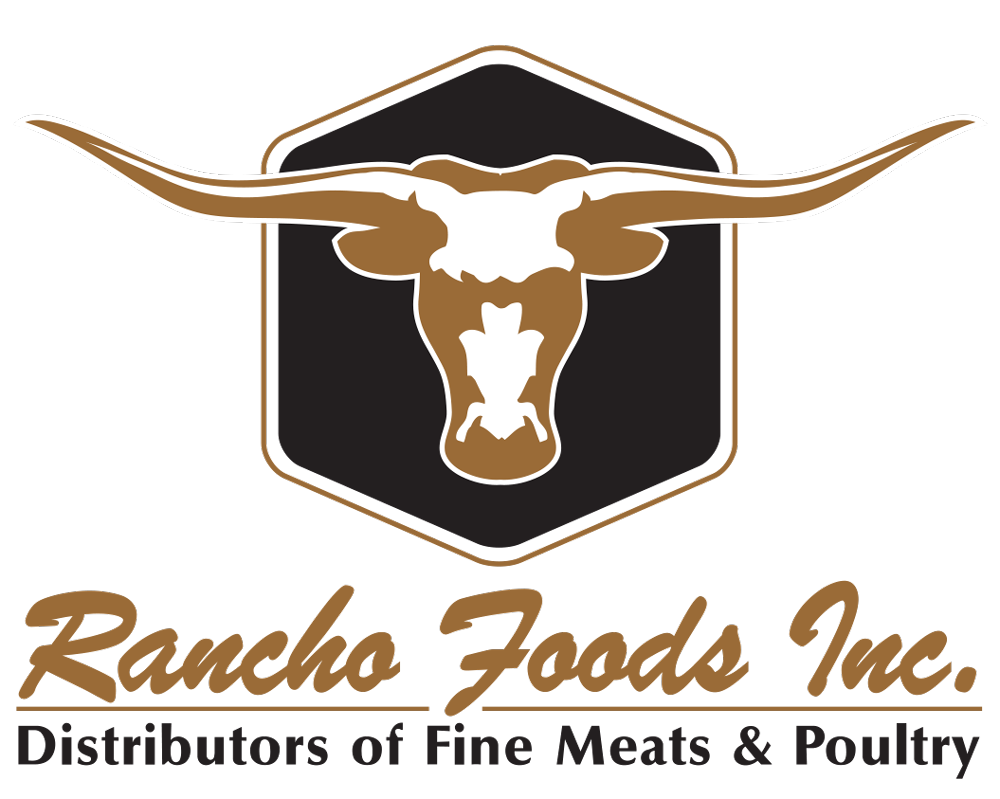
Rancho Foods
Food Distributor relies on strong partnership with Aspen Systems.
see more
Probably the most common question I get asked from an owner considering to move over to Canopy is, ‘Does it do what they say?’ My response to that is, ‘If they tell you it’s going to happen, it will happen – no questions asked.’ They stand behind everything. Their word is like gold.
Testimonial video regarding Aspen Systems
Document Imaging might easily pay for itself the one time you cannot locate proof-of-delivery using your manual paper retrieval system.
Frank Celano, Vice President

Rogers Poultry & Provisions
Poultry Processor values Canopy system and partnership with Aspen Systems.
see more
Aspen has a superior software package for the food industry, but it really comes down to the people that you need to deal with and rely on. Aspen treats their customers like family. Aspen is not a vendor to us… they are our partners, our friends. I know they will always do their best for Rogers Poultry.
Aspen treats their customers like family.
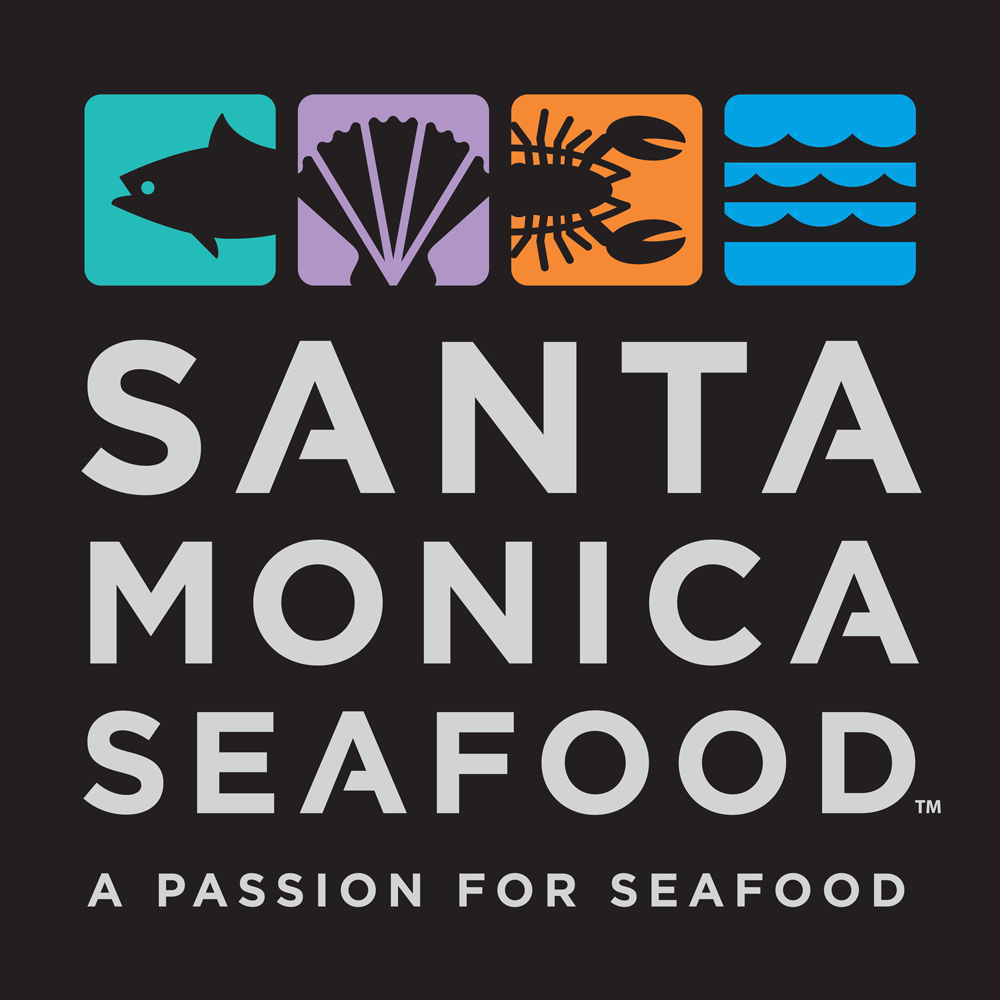
Santa Monica Seafood
Seafood Distributor enhances business efficiencies with Canopy.
see more
Canopy has proven time and time again to help Santa Monica Seafood increase data accuracy, optimize productivity, and brought countless efficiencies to our business operations.
As an example, Canopy’s Order Entry module automatically calculates the quantity that is available to sell for each product that a customer is ordering by taking into consideration incoming purchase orders, transfers, other orders, and raw material inventory. This information calculates instantly and tells our customer service department how much of the product they can sell without over selling it.
Canopy’s Dynamic Production feature has automated our production process from customer orders to our production floor. Key attributes such as raw material country of origin, vendor and purchase order flow automatically from raw materials to finished goods as we process seafood.
Prior to implementing Canopy, Santa Monica Seafood manually processed and calculated outbound freight load tendering and reconciliation, AP reconciliations, accruals, and AP Invoice approvals by using spreadsheets. With Canopy, we are able to process all of this in the software. This has saved our company over 10 hours per week in labor and brought more accuracy to our financial statements.
Aspen Systems’ Canopy software along with their skilled staff, is truly a winning combination for companies in the Food Industry!
Canopy has proven time and time again to help Santa Monica Seafood increase data accuracy, optimize productivity, and brought countless efficiencies to our business operations.
Frankie Celano, ERP Project Manager
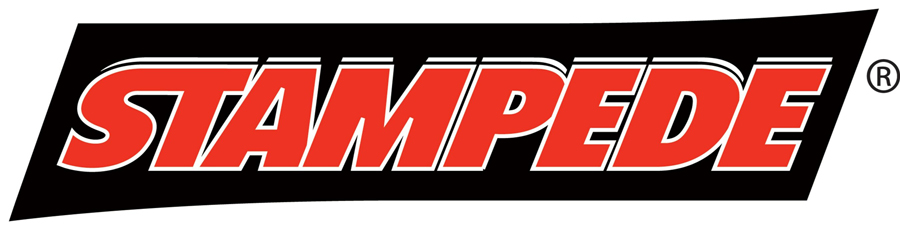
Stampede Meat
Meat Processor embraces challenge for Canopy implementation success.
see more
The ‘Purchase Order Inquiry’ screen gives one all the data they need to know about past, present, and future purchase orders. One can see who entered the purchase order, how much was ordered, how much was received, the unit price, etc. It is thanks to this screen that I can solve daily issues. I can easily tell if the correct weight was received, which warehouse the shipment was delivered to, or whether our unit price matches what we were invoiced.
We have hundreds of Aspen View reports, Event Watch Alerts, and Pulse Dashboards. Many of them were specifically created to help monitor and manage the real-time status of our orders.
Chad Bingham, Director of Information Technology
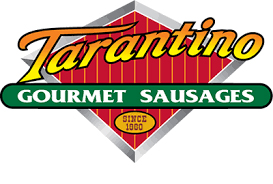
Tarantino Wholesale
Food Manufacturer & Distributor attributes business success and growth to Canopy’s reliability.
see more
Aspen Systems believes in the same core family values that Tarantino’s does. Both companies understand the importance of service and strive to create exceptional value. Every business has issues. What counts is how these issues are handled by your service company partners, and Aspen Systems handles our issues very well. We have partnered with Aspen Systems since 1988 and during that time, we have never failed to roll our trucks on time due to any failure attributed to Aspen hardware, software or service malfunction. I do not know anyone who can match this in the Food Industry.
The Production module allows Tarantino’s to manage raw material and finished product inventory for hundreds of formulas and recipes for spice, garlic, and sausage products.
Pete Tarantino, Sr., President
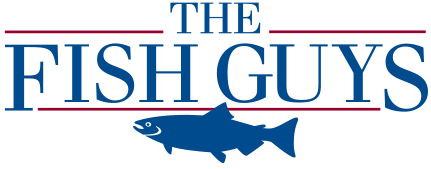
The Fish Guys
Seafood Processor with an ambitious business strategy nets operational efficiencies with Canopy.
see more
Canopy has completely changed the way that we do business because we can look at one computer screen instead of scrambling to call or e-mail each other to find the answers that we need. With the use of Pulse, Event Watch, and Aspen View Report Writer, anyone from any department can get the information that they need in a fraction of the time.
Testimonial video regarding Production
Testimonial video regarding CoPilot
Canopy has helped streamline our production processes, and has reduced mis-picks and credits while improving our on-time delivery to customers.
Kris Carlson, President & COO
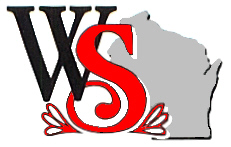
Wisconsin Spice
Spice Processor discovers great power in Canopy’s report writer, Aspen View.
see more
The customization that Canopy allows, specifically with Aspen Views, is a tremendous resource for our Company. With all the requirements for shipping on an international scale, conforming with food safety regulations, and meeting the needs of our customers, the use of Aspen Views and custom fields in aspects of almost every module has made Canopy an even more powerful resource for documentation required by our Company compared to the rigidness of other ERP systems.
The customization that Canopy allows, specifically with Aspen Views, is a tremendous resource for our Company.
David Bloomstrand, Operations Manager